あるQAマンの体験記 第11回 工程FMEAに初めて出会う!
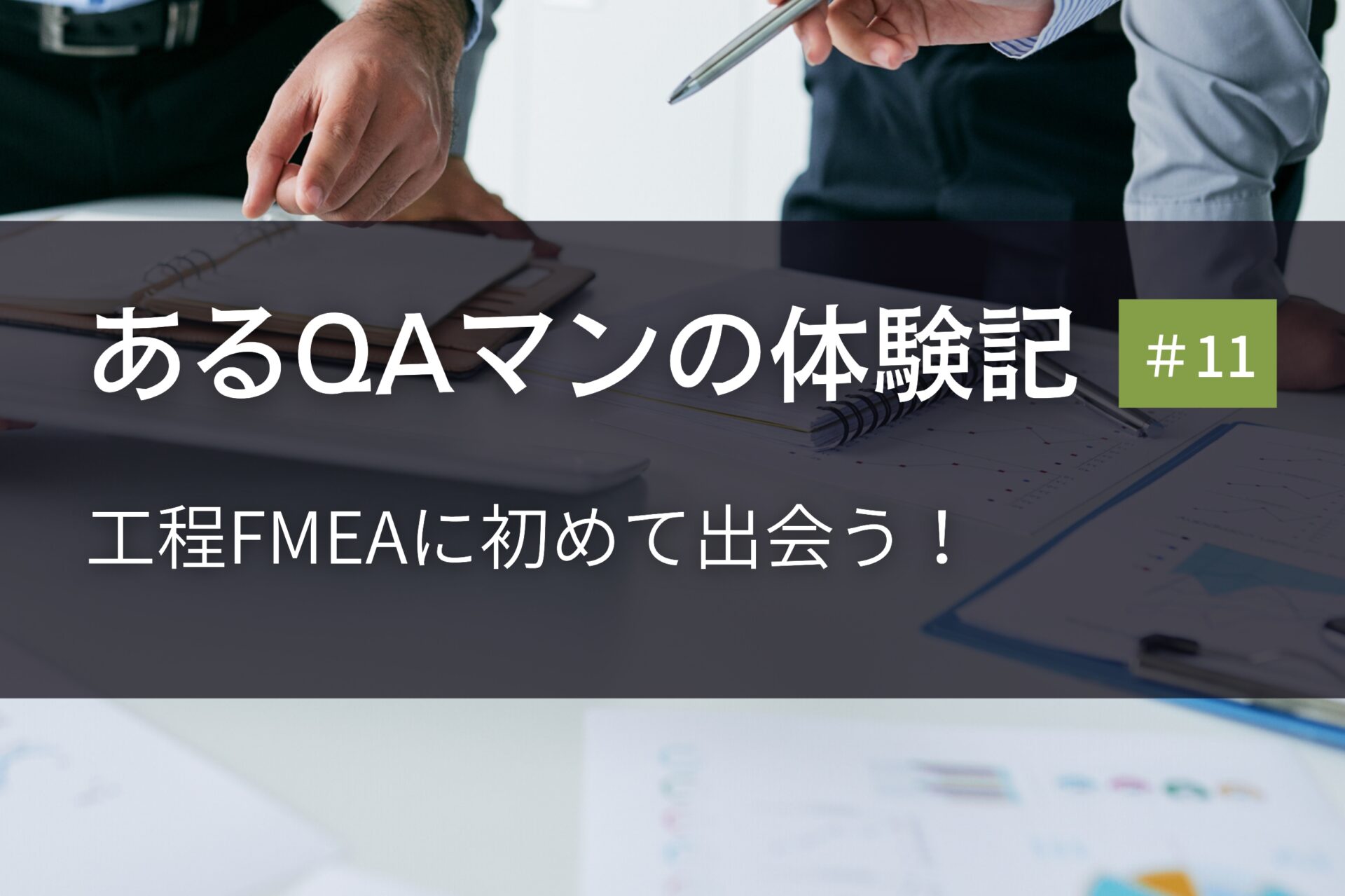
あるQAマンの体験記 第11回 工程FMEAに初めて出会う!
ロケットエンジン部品の製作は、単純な機械加工ではなく、ロー付け、溶接(溶融、電子ビームetc)、放電加工、熱処理、非破壊検査(X線検査、超音波探傷検査、浸透探傷検査etc)などのいわゆる特殊工程の塊であるといえます。工程が単純でないとそこで品質問題が起こる可能性がより高くなります。そういう観点から、ロケットエンジンの製作工程で、当時のNASDA(現在のJAXA)さんから工程FMEAを行うようにご指導を受けました。
今でこそ工程FMEAは、一般的な手法として使われるようになってきていますが、当時は、まだ新しい手法でした。具体的には、製造工程を最初から最後まで書き出し、各工程における製造上のリスクを評価し、リスクの大きい工程はあらかじめ対策を講じるというものです。
例えば特殊工程のロー付け作業では、次の観点から、不適合が発生するリスクをまず評価します。
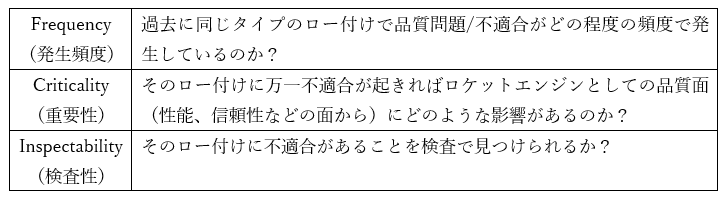
以上3つの観点から評価し点数化します。
発生頻度では、よく起きる不適合なら5点、めったに起きなければ1点とし、重要性では、その不適合でエンジンが止まるなら5点、影響がなければ1点とし、検査性では、検査で見つけるのが非常に困難なら5点とし、簡単に発見できれば1点などとします。
いずれも5段階で評価し5点と1点の間を4点、3点、2点とします。
そしてこれらを掛け合わせて点数が高いところは、過去の経験からよく不適合が発生し、万一その問題が起これば製品としての機能が損なわれ、検査でも発見しにくいということになれば、そのままの工程で放置するわけにはいきません。場合によっては、設計から見直し、あるいは、工程の手順の見直し不適合が発生しにくいロバスト性の高い工程にする、更に検査で不適合を検出できるように非破壊検査の追加などすることで、リスクを軽減することができます。
このような手法が、工程FMEAと呼ばれるもので、NASDAさんからは、これを実施するよう指導されました。特に工程に潜むリスクを顕在化し、3つの評価基準で掛け合わせ重要度を定量的に評価する(RPN: Risk Priority Numberといいます)ところに“なるほど”とうなったものです。
ノズルスカートというエンジン部品では実際にロー付けが適用されており、例えば、不適合発生頻度:3点、重要性:4点 検査性:5点 などとなり RPN=3x4x5=60ポイントでリスクはかなり高い工程になります。実際には、マイクロフォーカスX線探傷機という検査設備を新たに導入し、検査性の5点を2点まで下げる、プロセスを改善し発生頻度を2点にできれば、改善後のRPN=2x4x2=16ポイントまで低減できるというようなやり方です。
重点的にリスクの高い工程に事前対策を取るこの工程FMEAには、当時も興味を持って取り組んだ記憶があります。
最近では、自動車の品質マネジメントシステム要求であるIATF16949では、この工程FMEAが、コアツールとして標準化されています。また、航空エンジンメーカであるRR社やPWA社のサプライヤへの品質マネジメントシステム要求にも、この種の要求がすでに明文化されています。
品質問題が発見されてから対処することよりも、あらかじめリスクを顕在化させ、対策を先にとってしまういわば作り込み品質向上の打ち手としてこの工程FMEAが一般化してきていますが、四半世紀以上前にロケットの世界では、既に活用されていました。安全性、信頼性などの活動では、宇宙機器が最先端を走っており、学ぶところが大いにあると思います。
追伸
以前のメルマガで下記の通りFMEAを取り上げています。ご興味があればご参照していただければ幸いです。
コアツール解説-FMEA(航空機と自動車の品質マネジメントシステムの要求の違い)
文責 山本 晴久
「続き(第12回)を読む」
当社では主に航空宇宙の品質に関わるご支援をしております。
以下、リンクです。
・JIS Q 9100:2016 認証取得支援
・Nadcap 認証取得・更新支援
・JIS Q 9100:2016 規格解説セミナー
・JIS Q 9100:2016 内部監査員養成セミナー
・その他、お気軽にお問合せください。