航空機と自動車の品質マネジメントシステムの要求の違い 第5回
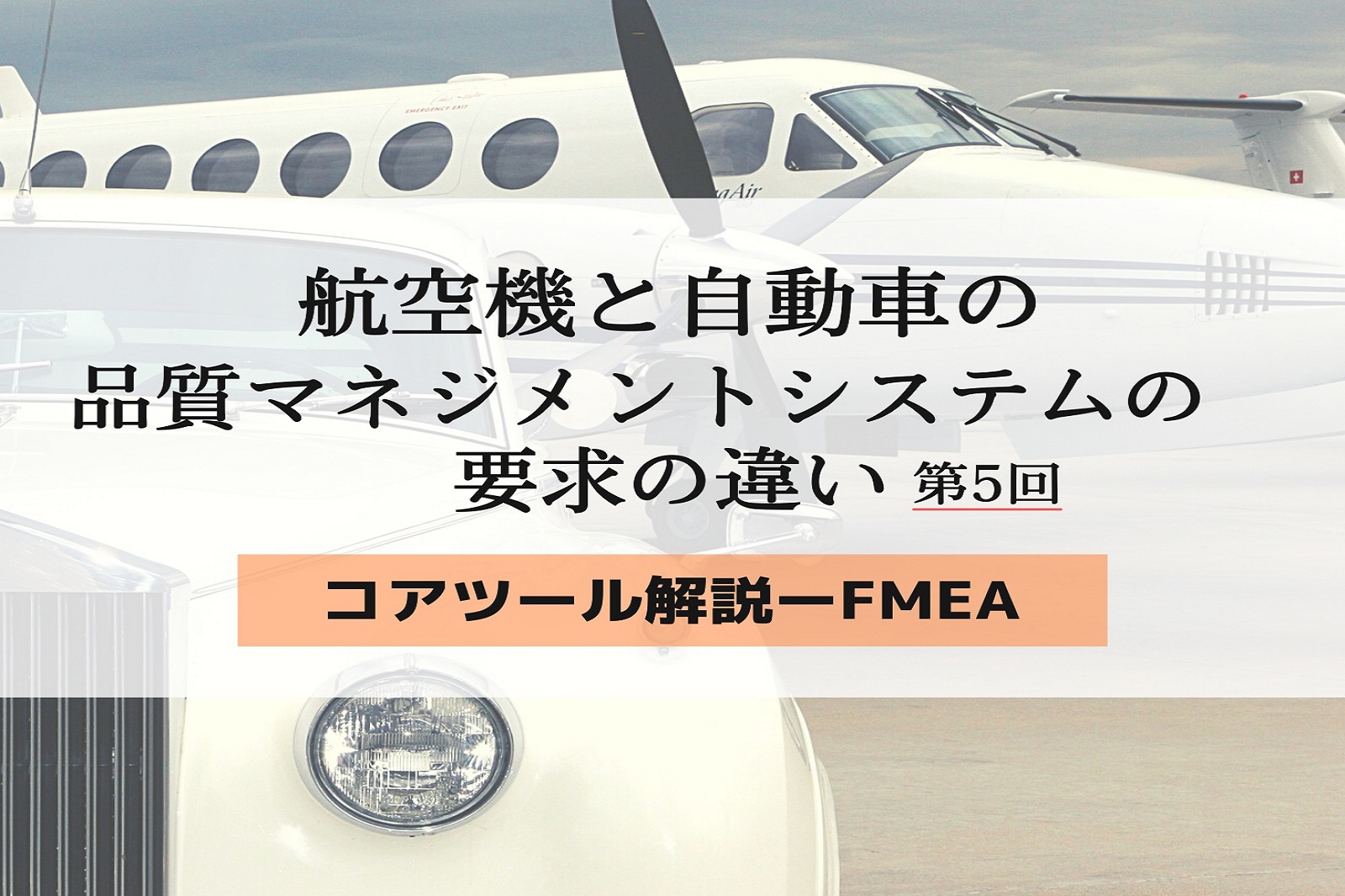
航空機と自動車の品質マネジメントシステムの要求の違い 第5回
今回は、コアツールの3つ目のFMEA (Failure Mode Effectiveness Analysis)について例を挙げてお話しします。FMEAは、故障モード影響解析といわれるものです。
このFMEAは、設計段階で実施されるものを設計FMEA(DFMEA)、製造工程設計段階で行われるものを工程FMEA(PFMEA)と呼んでいます。
前々回のコラムでも解説しましたが、FMEAとは
「設計又は工程の潜在的な故障モードをランク付けし、文書化してリスクを評価する。潜在的故障及びその影響の特定、要因(例えば、影響度(危険度)、発生頻度、潜在的故障の検出性など)のランク付け、リスクを低減する処置とその結果を評価する」というものです。
ここでは、FMEAに関し100円ライターを例にして説明しましょう。
**********************
100円ライターでどこかの部品が故障した時に、火がつかない、あるいは使っている人に危険があるかという観点で見てみましょう。
一つの例として、100円ライターでガスが不意に漏れるというときの故障モードを考えると、ガスが蓄えられない事象は、容器にあったクラックが進展してひびが入るケースがあります。
この場合のリスクをガスが漏れたときの影響度(危険度)、発生頻度、潜在的故障の検出性の3つの観点で評価をしてみます。
例えば、
・ガス漏れでライターは使用不可、万一引火の危険 →その影響度は5点(影響最大を5点満点)
・プラスチックだがひびはあまり入らない →発生頻度は2点(非常によく起こるを5点満点)
・外観検査で検出が何とか可能 →検出性は3点(検出が非常に困難を5点満点)
⇒これらを掛け合わせると5×2×3=30点になります。
これへの対策として
・部材を金属にし、ひびがめったに入らない →発生頻度は1点
・特別にクラックを見る検査を追加し必ず検出できる →検出性は1点
⇒影響度は5点のままでも5×1×1=5点となり、リスクは大きく減ります。
この30点とか5点を危険優先度(RPN=Risk Priority Number:各項目5段階で最大125点が最もリスク大)といっています。
実際には、ライターを設計する段階でRPNの高い故障モードから、設計改善を優先的に検討します。
上記の青字で示したような対策を取り、ひびが発生しないようにリスクをミニマムにしていきます。これを設計/工程FMEAと呼んでいます。
**********************
どうですか? FMEAを概念的にご理解いただけたでしょうか?
筆者も、ロケットエンジン開発の品質保証を担当していた時に工程FMEAをずいぶん熱心に行っていた記憶があります。ロケットエンジンは特殊工程の塊で、溶接、ロー付け、熱処理、表面処理、非破壊検査などが多用されており、FMEAは、本当にやりがいがありました。今となれば懐かしい思い出です。
文責 山本 晴久
「続き(第6回)を読む」
【e-learning】航空機の品質保証 ~自動車との比較理解~
航空機の品質保証の特徴や勘所について、航空宇宙製品に適用されている規格のAS9100の特徴と、自動車の品質保証を
比較しながら解説するオンライン学習を販売しております。
好きな時間に自分のタイミングで受講頂けます。興味のある方は、是非サンプルも試聴することができますので、
お気軽にお問合せ下さい。