あるQAマンの体験記 第12回 手探りでリスク管理の業務標準を作成!
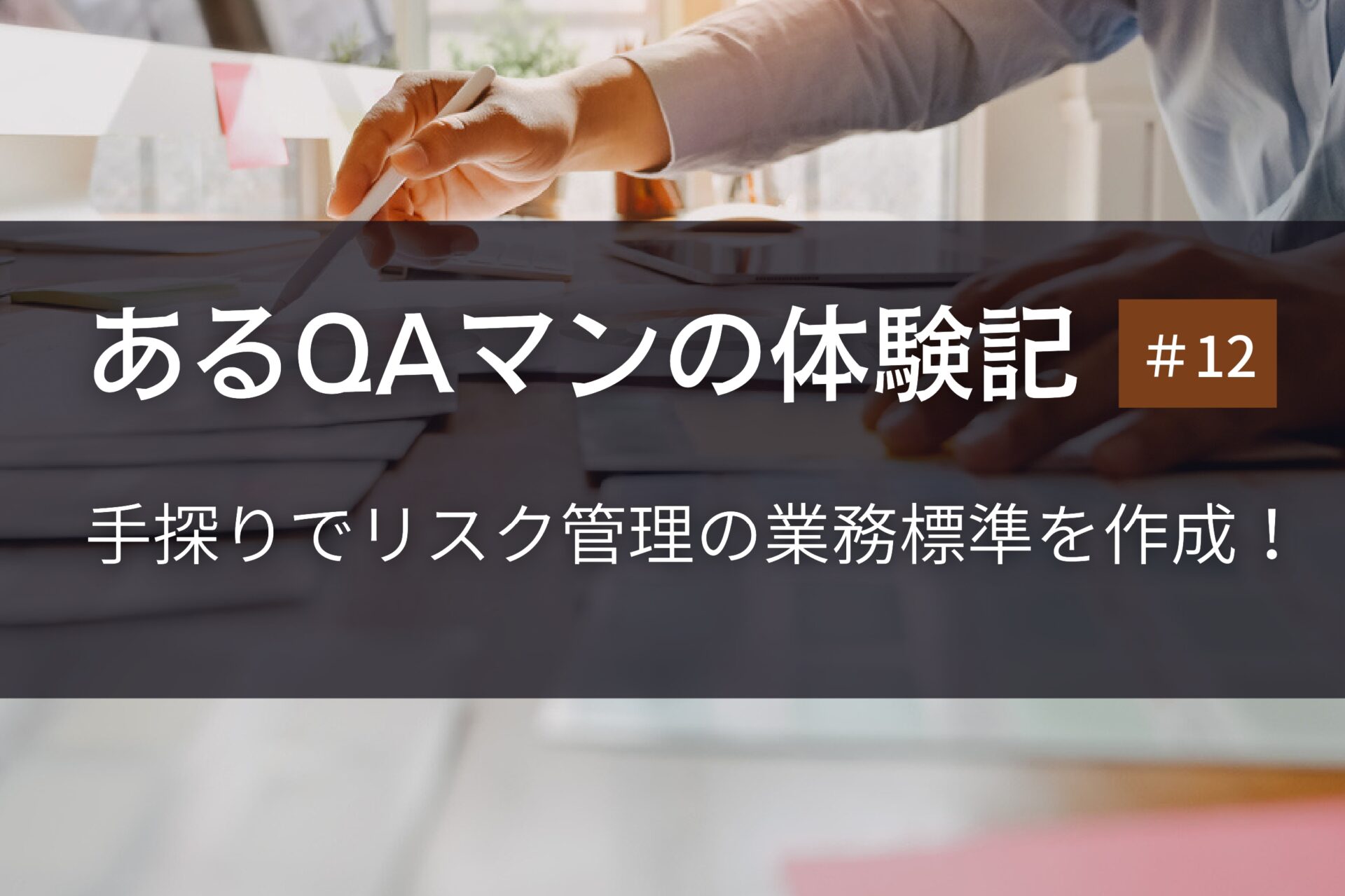
あるQAマンの体験記 第12回 手探りでリスク管理の業務標準を作成!
前回までの1~11回は、筆者が航空エンジン、宇宙エンジンなどの部品を製造している工場で検査計画業務を担当していた入社から6年くらいの期間に経験したことを書いてきました。
その後、職場変更になり検査課から品管部管理課という部の全体を統括するところに移りました。これからは数回に亘り、ここで経験したことを書きたいと考えています。
先ず、今回はリスク管理です。
当時(40年近く前です)は、筆者のいた職場では、航空宇宙製品の開発と製造が行われていました。具体的には、当時の防衛庁(今は防衛省)向け回転翼機の開発、練習機/実験機の開発、ミサイルの開発、そして当時のNASDA(今はJAXA)向けの宇宙ロケットの開発などが行われていました。
これら大規模システム製品の開発では、新しい設計技術、新しい製造技術が採用されるため、ここに技術的なリスク(JISQ9100では運用リスクと呼んる)があるという考え方で、いかにしてリスクを顕在化し事前につぶしていくかが議論されていました。当時その工場では、リスク検証/軽減の活動をリスク管理活動と名付け、既にいくつかの製品開発で取り組んでいました。進め方は、概ね以下のようなものでした。
*******
各部門で新しい技術でリスクがあると考えた事項を1点1葉でリスク管理表に書き出し、自らそのリスクを評価する。具体的には、リスクの大きさを未検証度(発生確率)と日程への影響度(システムへの影響度)との2つをポイント化し、それぞれ3点満点とし、2つの指標を掛け合わせて、最大9点、最小1点で評価し、それぞれ検証計画を立て、検証が完了していけば、点数が下がるというものです。このリスクを点数化したものをRPN(Risk Priority Number)と言っています。
例えば、ある構造をアルミから複合材に変えたとします。未検証度は全く新しい工程であり、3点とします。また、日程への影響度などは、製造の工期が比較的長いので2点とします。この場合のRPNは、3×2=6点となります。複合材の試作を繰り返し、製造工程が安定したことで未検証度が1点になれば、RPNは、1×2=2点となり、4点分のRPNが減少したことになります。
そして例えばリスク管理対象が100件あり、トータル580点のリスクが、開発が進む過程で検証が順次進み、残リスクポイント(トータルのRPN)が減少していくというものです。
この管理をリスク検討審議会のようなもので管理していく訳です。審議会の取りまとめ者は、設計部門のプロジェクトマネージャなどにお願いし、プロジェクトマネージャが出席しない限り審議会を開催しないということで運用していました。
この活動の特徴は、各部門の担当者が、他部門が抽出したリスクを共有化できること、リスクを放置せずに、検証計画を立てて、各部門が共同してリスクを潰していくところ、また残リスクポイントをグラフ化することで視認性を上げることなどでした。
*******
そしていくつかのプロジェクトで、それぞれのやり方で運用していたリスク管理を事業所レベルの業務規程として制定することにしました。
関係する部門が多いこと、工場もいくつかに亘ることなどから、すべての分野からの意見を調整することは非常に困難でしたが、戦闘機屋からミサイル屋、宇宙ロケット屋も含めて主としてプロジェクト設計のメンバー、生産技術と品証にメンバーにも意見を聞いて規程を作成しました。1年くらいの時間をかけて取り組んで標準化できたことで非常にやりがいのあるものでした。
今、JIS Q 9100で運用リスクとして製品のリスク軽減活動を要求されていますが、当時行っていたリスク管理管理活動は、いわば先取りした活動であったと言えるでしょう。
文責 山本 晴久
当社では主に航空宇宙の品質に関わるご支援をしております。
以下、リンクです。
・JIS Q 9100:2016 認証取得支援
・Nadcap 認証取得・更新支援
・JIS Q 9100:2016 規格解説セミナー
・JIS Q 9100:2016 内部監査員養成セミナー
・その他、お気軽にお問合せください。