航空機と自動車の品質マネジメントシステムの要求の違い 第3回
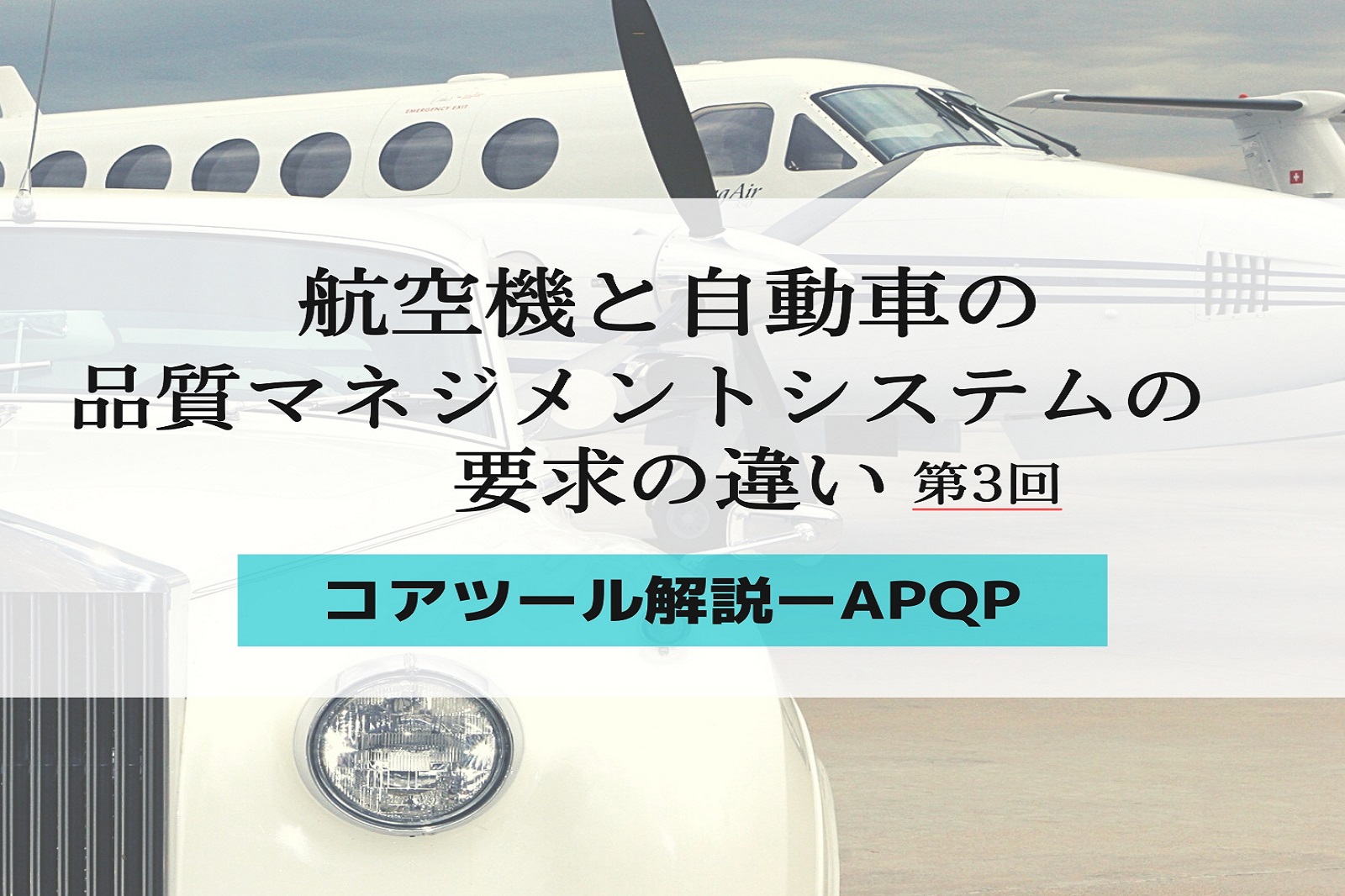
前回は、製品の使われ方とその生産の方法などからIATF16949(自動車)とJISQ9100(航空機)を対比してその特徴を少し解説しました。IATF16949では、AIAG(全米自動車産業協会)が参考文献としてコアツールをレファレンスマニュアルとして定めています。
今回から5回に亘り、このコアツールについて簡単に解説を試みたいと思います。
5つのコアツールとは、次のものをいいます。
(1)APQP (Advanced Product Quality Planning):先行製品計画
(2)PPAP (Production Part Approval Process):生産部品承認プロセス
(3)FMEA (Failure Mode Effectiveness Analysis):故障モード影響解析
(4)SPC(Statistical Process Control):統計的工程管理
(5)MSA (Measuring System Analysis):測定システム解析
先ず、今回はAPQP(先行製品計画)を取り上げます。
APQPは、5つのフェーズを規定しています。(⇒以下が主要な実施事項です)
フェーズ-1:プログラムの計画・定義
⇒マーケティング゙、ベンチマーク、設計/信頼性/品質目標など開発製品の計画
フェーズ-2:プログラムの設計・開発
⇒設計FMEA(設計リスク評価に基づきトラブルを起こしにくい設計)、DFM/DFA(製品の作りやすさを考慮した設計)、設計審査、試作CP(コントロールプラン:QC工程表と同義)、図面/技術仕様書など設計の詳細決定
フェーズ-3:プロセスの設計開発
⇒プロセスフロー図、工程FMEA(製造リスク評価に基づく生産設計)、量産試作CP、MSA(計測システム解析)計画、工程能力調査など生産設計実施
フェーズ-4:製品・プロセスの妥当性確認
⇒MSA、SPC(統計的品質管理)、量産CP、量産の妥当性確認、PPAPなど製造の妥当性確認
フェーズ-5:量産・改善
⇒CS向上、教訓の活用、引渡/サービス改善など
以上のフローを図にしたものが下記の図です。
フェーズ-1からフェーズ-5までが新しい自動車を世の中に送り出す際の「製品企画から試作/開発設計、製造プロセスに関わる生産設計、そして量産初期の製品妥当性確認、更に量産と市場での運用、そして改善」という開発からライフサイクル全般に亘り、品質、コスト、納期の面でお客様の満足を得るために必要最低限の実施事項のすべてが、このAPQPの要求の中には、含まれていると考えられます。
ここでは紙面の都合上個々の内容に関して詳しくは解説できませんが、APQPの要求の全体のイメージを掴んでいただければ幸いです。
次回は、PPAPの解説をします。
文責 山本 晴久
「続き(第4回)を読む」
【e-learning】航空機の品質保証 ~自動車との比較理解~
航空機の品質保証の特徴や勘所について、航空宇宙製品に適用されている規格のAS9100の特徴と、自動車の品質保証を
比較しながら解説するオンライン学習を販売しております。
好きな時間に自分のタイミングで受講頂けます。興味のある方は、是非サンプルも試聴することができますので、
お気軽にお問合せ下さい。