あるQAマンの体験記 第3回 実験計画法に初めて触れる!
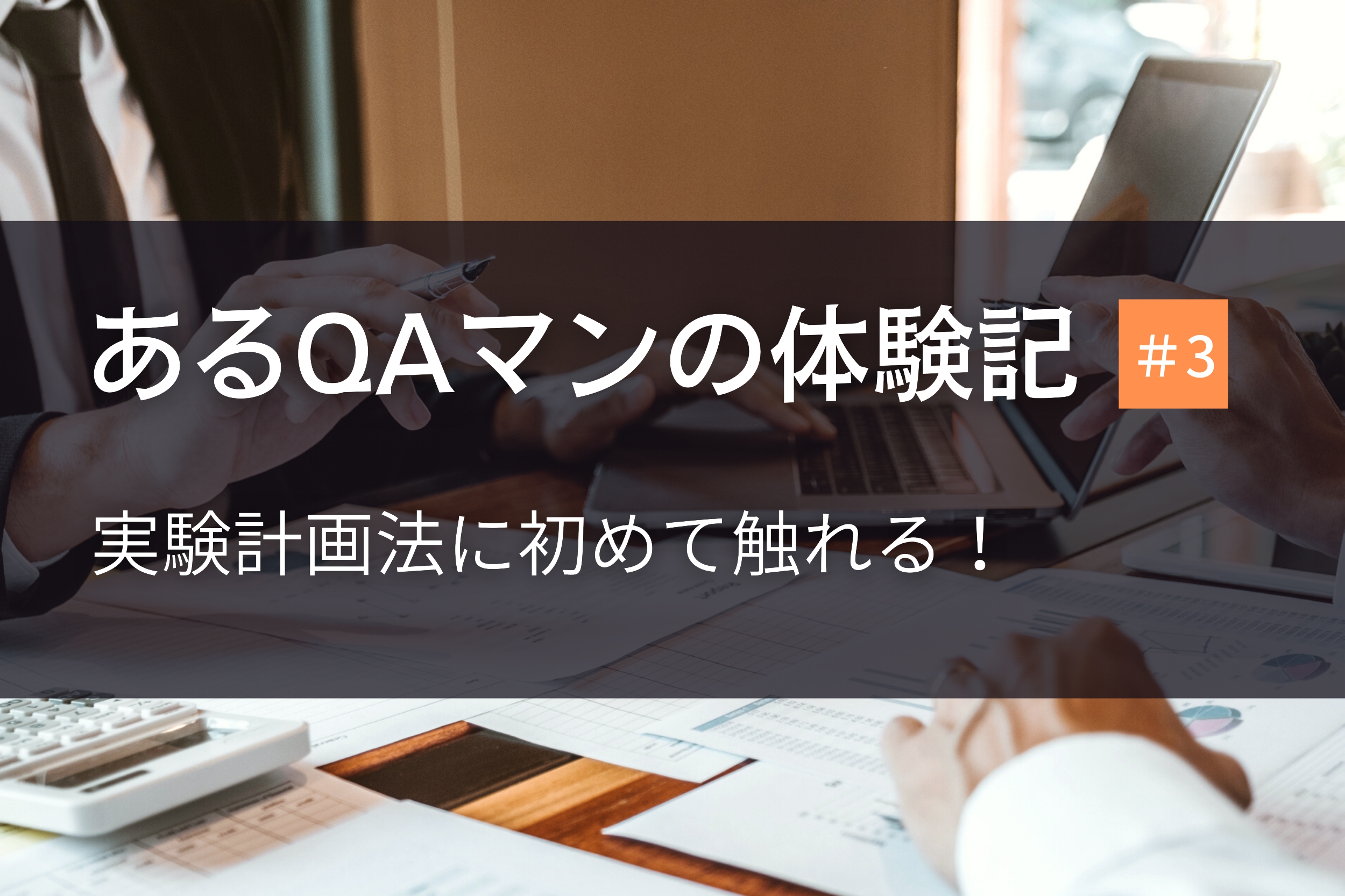
今回は、生産時に品質問題が発生した時の原因探求の手法の一つとして使われる実験計画法を使ったときの経験談です。
実験計画法という手法は、統計学を使った手法です。
ある品質特性に影響するパラメータ(条件)は、複数あることが一般的で、どのパラメータの変動がどの程度品質特性に影響するかを実験で求めるには、パラメータを振り分けながら数多くの実験をしなければなりません。
例えば、パラメータが3つあって、それぞれに3つの水準を設けて実験しようとすると、3×3×3=27回で且つデータにはばらつきが出るので各3回データ取りすると27回×3回=81回の実験をしなければ最適の条件が見つからないことになります。これを何とか統計的に効率的に処理できないかと考えた人がおられました。
英国のフィッシャーという人がその方で、農業実験を科学的に、合理的に行うために実験計画法を開発したとされています。すべてのパラメータ条件を総当たりすることなく、いくつかの代表的なパラメータと水準を組み合わせて実験し、そのデータを統計的に分析することで、どのパラメータのどの水準がもっとも適した条件かを評価する手法です。英語では、DOE(Design of Experiment)と呼ばれており、6シグマ活動では分析手法で重要な手法となっています。
ところで筆者が経験した実験計画法との初めての出会いを紹介します。
ある時製造工程でトラブルが起きました。エンジン部品生産の研削工程で研削した部品が浸透探傷検査で次から次へと研削割れが発見されました。
研削割れを起こす要因(パラメータ)はいろいろあると考えられました。具体的には、部品素材のロットごとの材料特性の変化、研削加工条件(研磨代、研磨速度)の変化、研削油の変化、砥石の再研磨のサイクルの変化など多岐にわたることが考えられました。
この時にこれらの要因で何が研削割れに効いているかを実験で検証しようという話になりました。実際に試験をしようとして要因毎の試験を組み立てようとして、はたと困ってしまいました。あまりにも要因が多くて膨大な試験をしなければならないからです。
そこで実験計画を使おうということになりました。当時は同じ品質管理部に統計処理の専門家がおられて、早速工場に出向いてもらい、実験計画法での要因の振り方など教えてもらい、指導を受けながら原因探求の試験を行いました。
当時は、パソコンもない時代で分散分析を電卓で計算し、何とか原因を特定することができました。参考にこの時の結末は、素材起因で研削割れが発生したというのが原因であることが分かり、トラブルシューティングも無事終わりました。
品質問題って大変だなぁ・・・、問題がなければ楽でいいのに・・・と思っていましたが、今にして思えば、自分達が成長できる素晴らしい機会をその都度、得ていたのだと思います。そして、今では、むしろ楽しい思い出にもなっています。
また、現在、航空関連のメーカなどででよく使われているMINITABなどの統計ソフトを使えば、処理はいつでも簡単にできるようになっていますが、自分の手で計算し分析した経験があってこそ、そのソフトを使いこなせるのかもしれないと思ったりもしています。
単に手法を使えるということだけでなく、どういう考え方で、その手法で分析できるかまで知っておくことは大切だと思います。
文責 山本 晴久
「続き(第4回)を読む」
当社では主に航空宇宙の品質に関わるご支援をしております。
以下、リンクです。
・JIS Q 9100:2016 認証取得支援
・Nadcap 認証取得・更新支援
・JIS Q 9100:2016 規格解説セミナー
・JIS Q 9100:2016 内部監査員養成セミナー
・その他、お気軽にお問合せください。