あるQAマンの体験記 第26回 トラッキングシステム
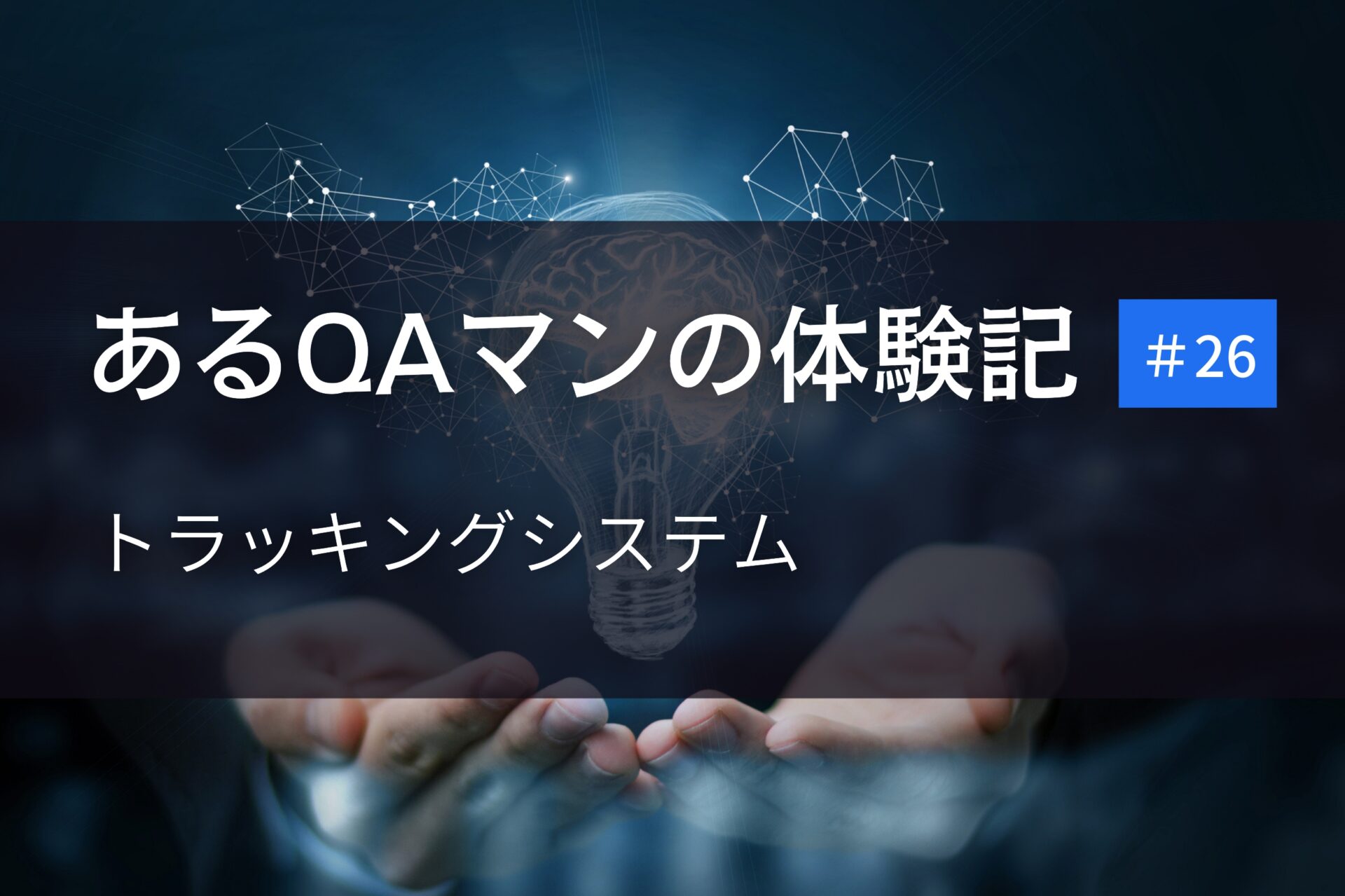
フィリピンの工場で大きな品質問題が発生した時の対策に関して少し話をしたいと思います。
スピンドルモーターの最終組立は、製造ラインがあり20m位の長さ(2本で一組の製造ライン)があって、組立と検査の工程が15工程ほど並んでおり、各工程には作業者が20人近くラインの両側に張り付いていました。
作業者のスキルを管理するために作業着の背中に担当できる工程番号を貼り付け、作業者が抜けたときは、ラインリーダがすかさずそこには入るような管理をしていました。作業は基本的には手作業ですが、試験は、自動で行われデータは記録されるようになっていました。
ここで起きた問題は、試験工程が飛ばされたものがあって、それが発見できなかったというものでした。整斉と流れているときは問題ないのですが、設備の異常や品質問題などが発生してラインが乱れ、変動作業などがあるとこのような工程飛ばしが起こりうるリスクがありました。客先からも即時の対策を求められました。
そこで本社の設備/生産技術者、システムエンジニアなど数名に現地に緊急で来てもらって是正対策チームを作りました。対策はいろいろ検討されましたが、結果として採用されたのは、下記のようなものであり工程を通過した毎に2次元バーコードでデータを読み、且つ検査工程では、データの判定と保存を行うことにしました。そしてその組立品のバーコードを梱包前に読み、工程飛ばしがないことと試験データに異常がないことを判定して、PCの画面に合否判定をできるようにしました。下記の流れ図を参照ください。
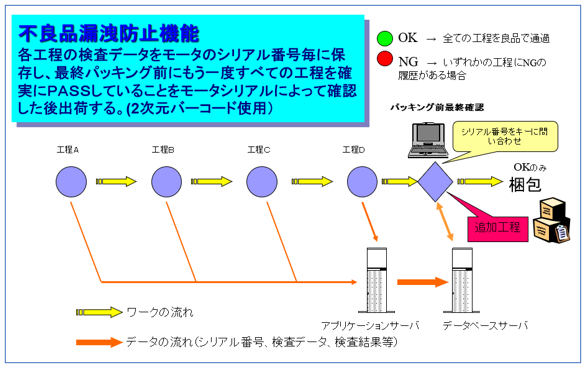
このシステムをトラッキングシステムと呼び、問題の起こりうるラインに順次適用していきました。当時、QRコードやバーコード、更にICチップを利用するなどして製品毎の管理や物の位置を検出する管理などが一気に進むところを経験しました。
トラブルシューティングの本質は、原因を特定し、それを取り除く手段を検討して、最善の手を打つことですが、データ処理などの技術が進むと従来では考えられなかったようなロバスト性の高い対策も取れるようになりました。
この対策は、検討から実現まで1か月程度で完了しましたが、お客様からは、迅速な対応にお褒めの言葉を頂きました。本社から来ていただいたメンバーも安堵して戻っていきました。何事もスピードが大切と思った次第です。
文責 山本 晴久
当社では主に航空宇宙の品質に関わるご支援をしております。
以下、リンクです。
・JIS Q 9100:2016 認証取得支援
・Nadcap 認証取得・更新支援
・JIS Q 9100:2016 規格解説セミナー
・JIS Q 9100:2016 内部監査員養成セミナー
・その他、お気軽にお問合せください。