あるQAマンの体験記 第7回 ブレード検査におけるハードポイント方式の採用
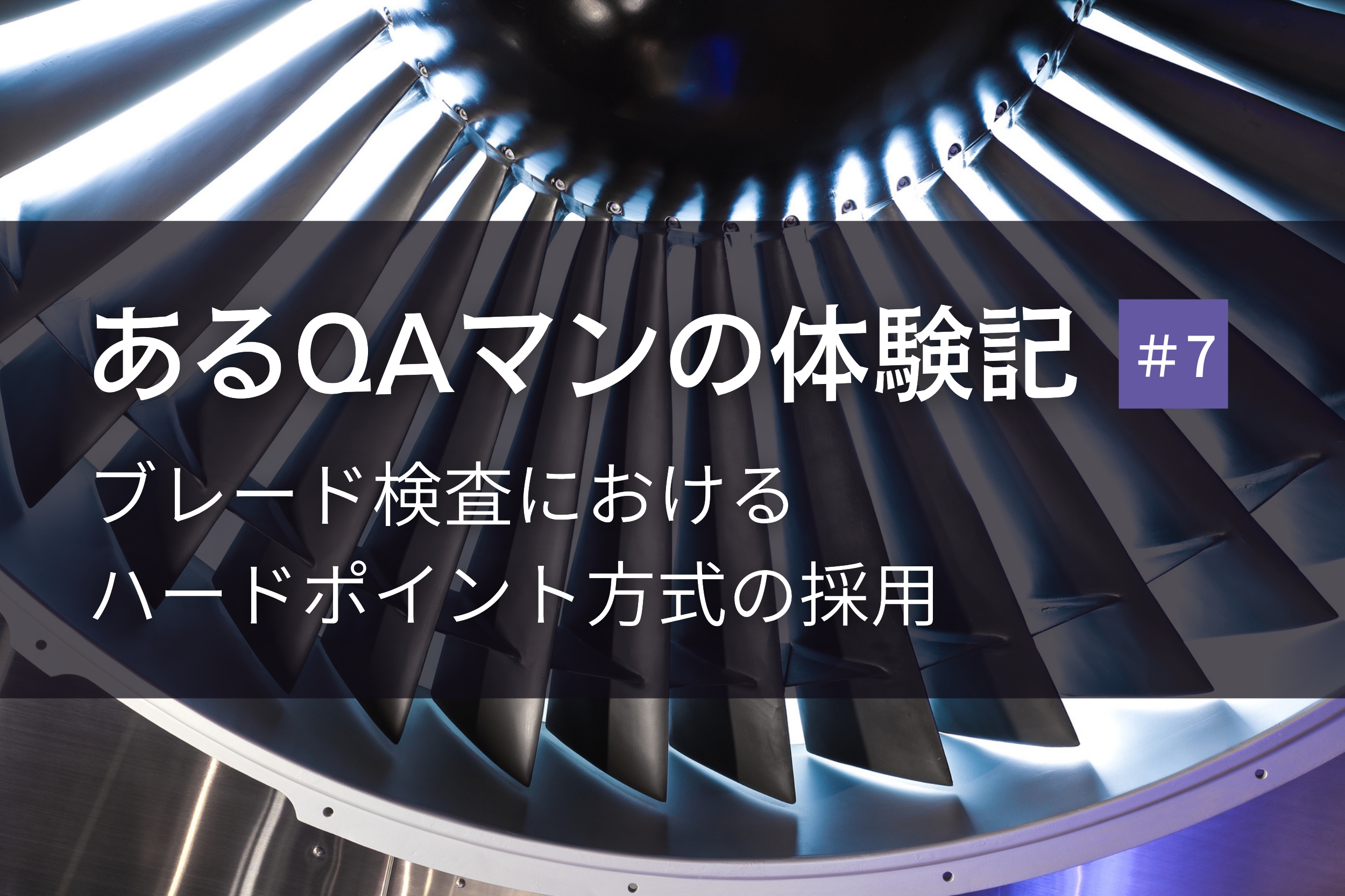
エンジンの部品の中でもタービンブレードの検査を担当していた時の話です。ブレードは、エンジン部品を組み立てる段階で、タービンディスクという部品に、段数にもよりますが、60~70個のブレードを組み込んで使われるものです。
翼面は加工せず、ディスクに埋め込むルート部と言われる個所と、翼の外周にあたるシュラウド部という個所を加工するものです。ブレードは、加工/検査基準を三次元形状の複雑な曲面を持つ翼面から作り出さなければならないので加工も検査も難しい部品です。
筆者が担当していたタービンブレードは、インコネルという耐熱合金の材料からできており、精密鋳造という手法で作られていたものでした。製法としてはロストワックス法で作られていました。
ロストワックス法というのは、ブレードの実体の形状をワックス(蝋)で作り、砂で表面を固め、ワックスを外に流し出し、できた空間に高温で溶かした金属を流し込んで固めるという手法であります。このロストワックスで作られた鋳造品は、精度が高く、かつて芸術品の製造などにも使われてきた手法と言われています。
先程、ブレードの加工/検査が難しいのは取り付けの基準を翼面から作り出さないといけないからだと言いましたが、筆者が入社した頃は、ギロチン方式と呼ばれる方式で加工/検査の基準を決めていました。
具体的には、翼面から加工/検査基準を作り出すギロチン方式は、先ず翼長方向を1点で決め、翼の2つの断面(A、B)で翼形状から翼の背側、腹側のテンプレートを使ってベストフィットになるようにブレードの位置を決めていく方式で、位置決めに時間がかかるものでありました。(図-1参照)また、作業者のスキルが必要で取り付けにもばらつきが発生しやすいものでした。
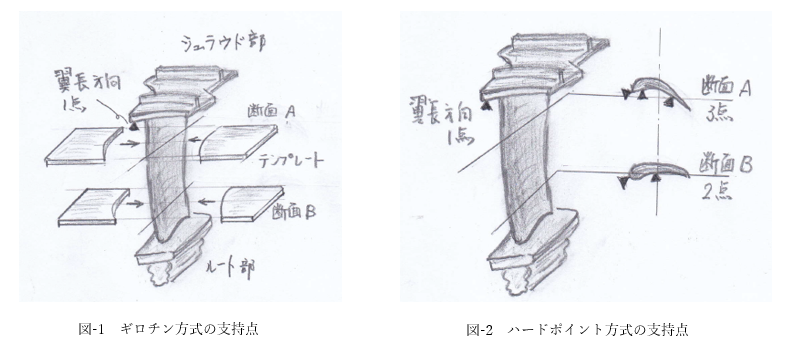
その方式がハードポイント方式に代わった訳です。ハードポイント方式では、翼面形状全体を使って基準を決めるのではなく、ポイント(ツールポイントなどという)で受けるものでありました。具体的には、ギロチン方式と同じく翼長方向を1点で決めますが、翼面からの基準出しは、形状全体から決めるのでなく、翼のある断面(A断面)で前縁と腹側の2点、もう一断面(B断面)で前縁と腹側1点、翼長方向も含め6ポイントで位置決めすれば基準が作れるというものでした。(図-2参照)
この方式によれば、加工及び検査では、画期的に位置決めの時間を短くでき、また位置決めに個人のスキルが入り込むことがなくばらつきも小さく抑えることができました。
これが可能になったのは、翼面の精度そのものが以前よりもよくなったもので、翼の代表点で基準を取っても位置決めに問題が出ないと判断されたためだと考えられます。筆者は、この基準が変更になったことで必要な検査治具などを考案し、検査できるようにセットアップすることになりました。
これを入社一年目に簡単な論文を(登用論文といっていた)まとめて提出しました。
図面の規定が変わり、そのための検査手段を準備することになったが、非常にいい経験でした。
この検査を通じて、時代と共に設計の考え方、製造の考え方、検査の考え方もどんどん変わっていくのだということを実感することができました。
今では、出身会社の資料館に古いタイプのギロチン方式のゲージが飾られています。時々見ては懐かしく思っています。
文責 山本 晴久
「続き(第8回)を読む」
当社では主に航空宇宙の品質に関わるご支援をしております。
以下、リンクです。
・JIS Q 9100:2016 認証取得支援
・Nadcap 認証取得・更新支援
・JIS Q 9100:2016 規格解説セミナー
・JIS Q 9100:2016 内部監査員養成セミナー
・その他、お気軽にお問合せください。